Understanding the Process of Magnetic Particle Testing: A Step-by-Step Guide
Pr
Introduction to Magnetic Particle Testing
Magnetic Particle Testing (MPT) is a non-destructive testing method used to detect surface and near-surface discontinuities in ferromagnetic materials. This technique is widely utilized in various industries, including automotive, aerospace, and construction, due to its effectiveness in identifying flaws that could potentially lead to failure. Understanding the step-by-step process of MPT can help ensure the integrity and safety of critical components.
MPT works by magnetizing the material being tested and then applying ferrous particles to its surface. Any discontinuities in the material will create a leakage field that attracts the particles, forming a visible indication of flaws. This guide will walk you through the detailed process of Magnetic Particle Testing.
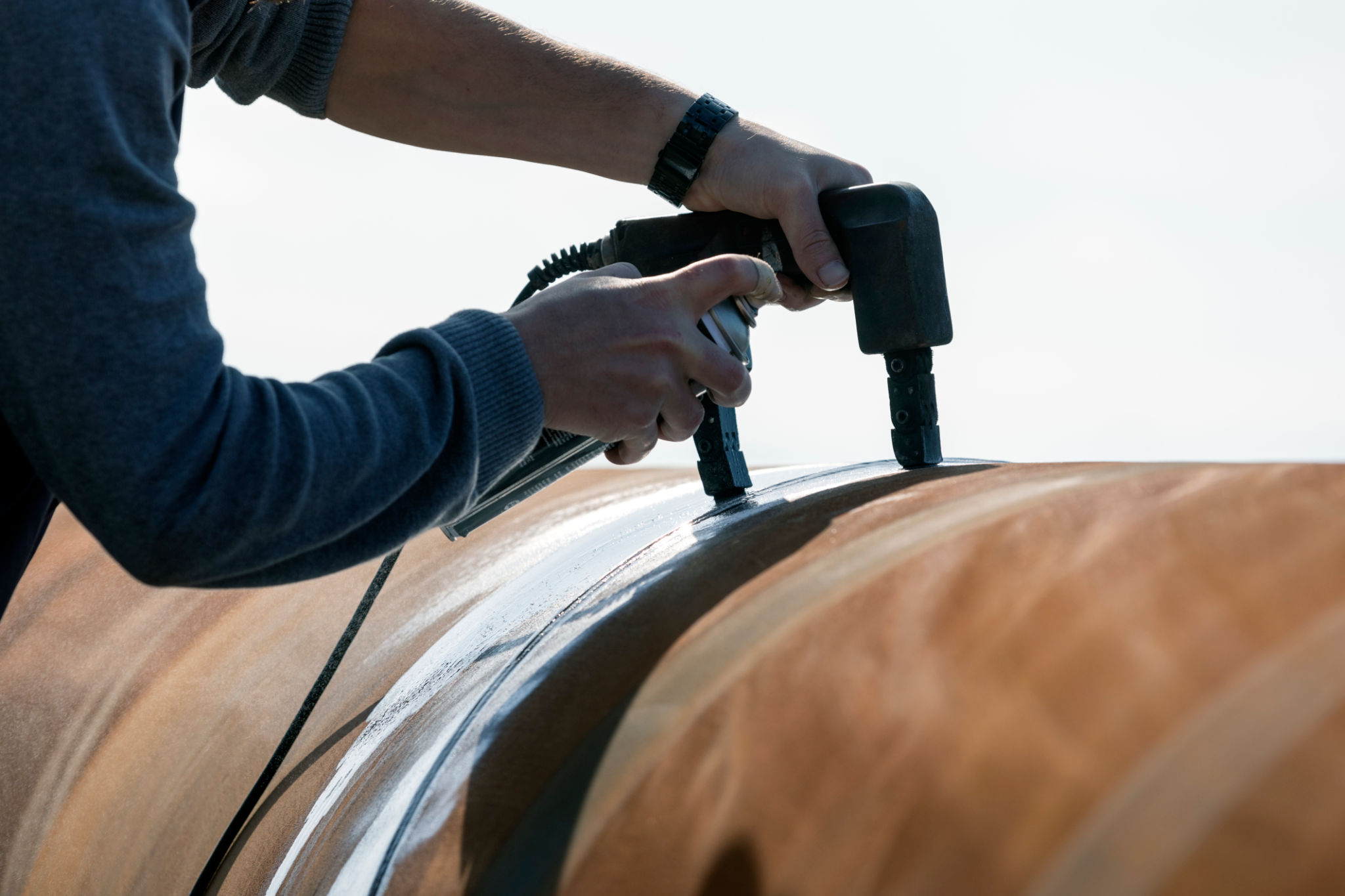
Step 1: Surface Preparation
The first step in MPT is preparing the surface of the material to be tested. It is crucial to clean the surface thoroughly to remove any dirt, grease, or paint that could interfere with the test results. A clean surface ensures that ferrous particles can adhere properly to any leakage fields created by discontinuities.
In some cases, light sanding or grinding may be necessary to remove coatings or surface irregularities. It is important to note that the surface should be dry before proceeding to the next step, as moisture can affect the distribution of magnetic particles.
Step 2: Magnetization
The next step involves magnetizing the component. This can be done using different techniques such as direct magnetization, where an electric current is passed directly through the component, or indirect magnetization, using a yoke or coil. The choice of method depends on the size and shape of the component, as well as the specific requirements of the inspection.
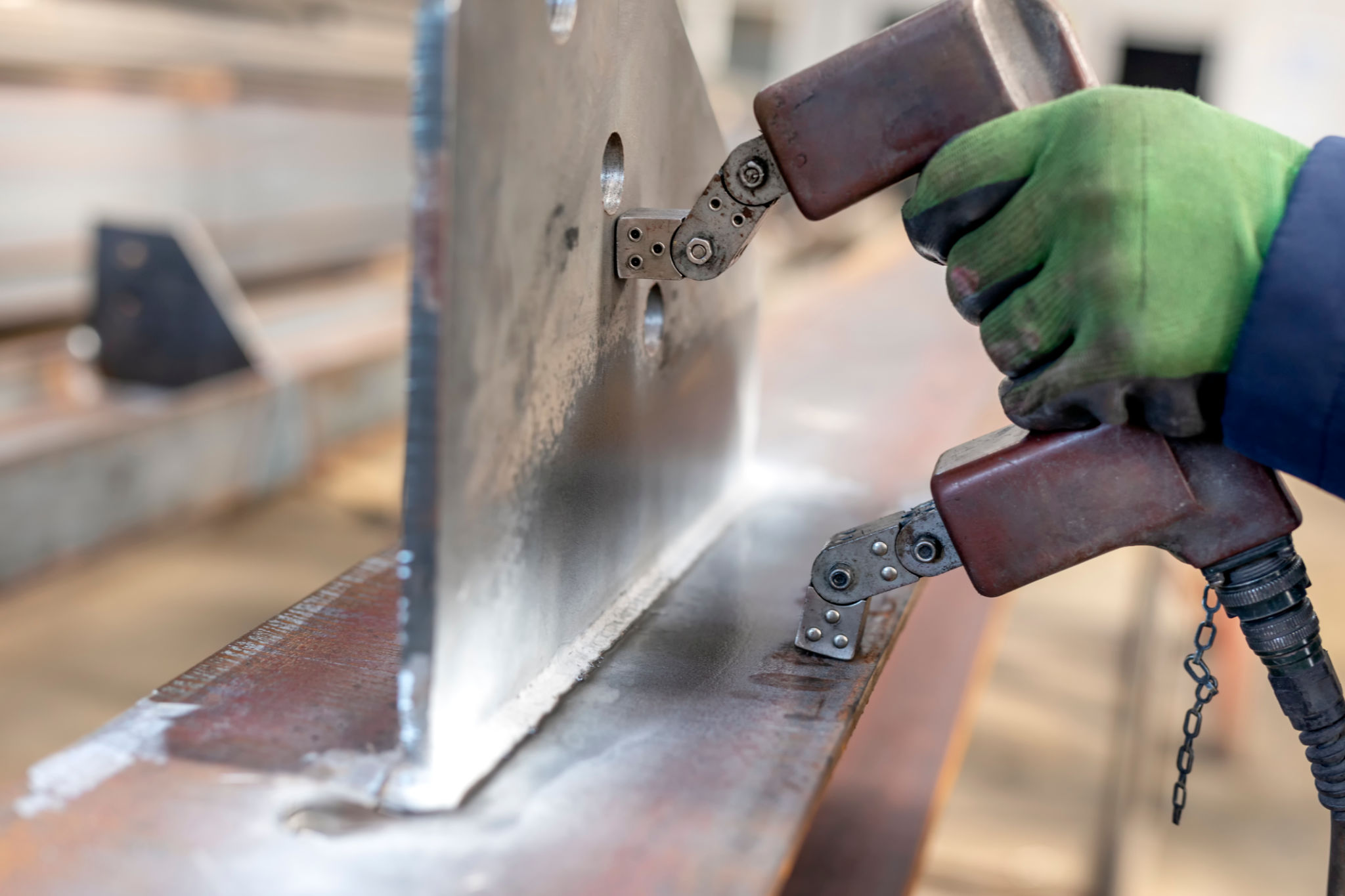
Magnetization should be strong enough to ensure that any discontinuities create a significant leakage field but not so strong that it causes excessive particle build-up. The key is to achieve an optimal balance for accurate detection.
Step 3: Application of Ferrous Particles
Once magnetized, ferrous particles are applied to the surface of the component. These particles can be either dry or suspended in a liquid carrier, depending on the testing environment and component characteristics. Dry particles are typically used for rough surfaces, while wet particles are preferred for smoother finishes.
The application should be done uniformly to ensure full coverage of the area being inspected. The particles will cluster around any leakage fields caused by flaws, making them visible under proper lighting conditions.
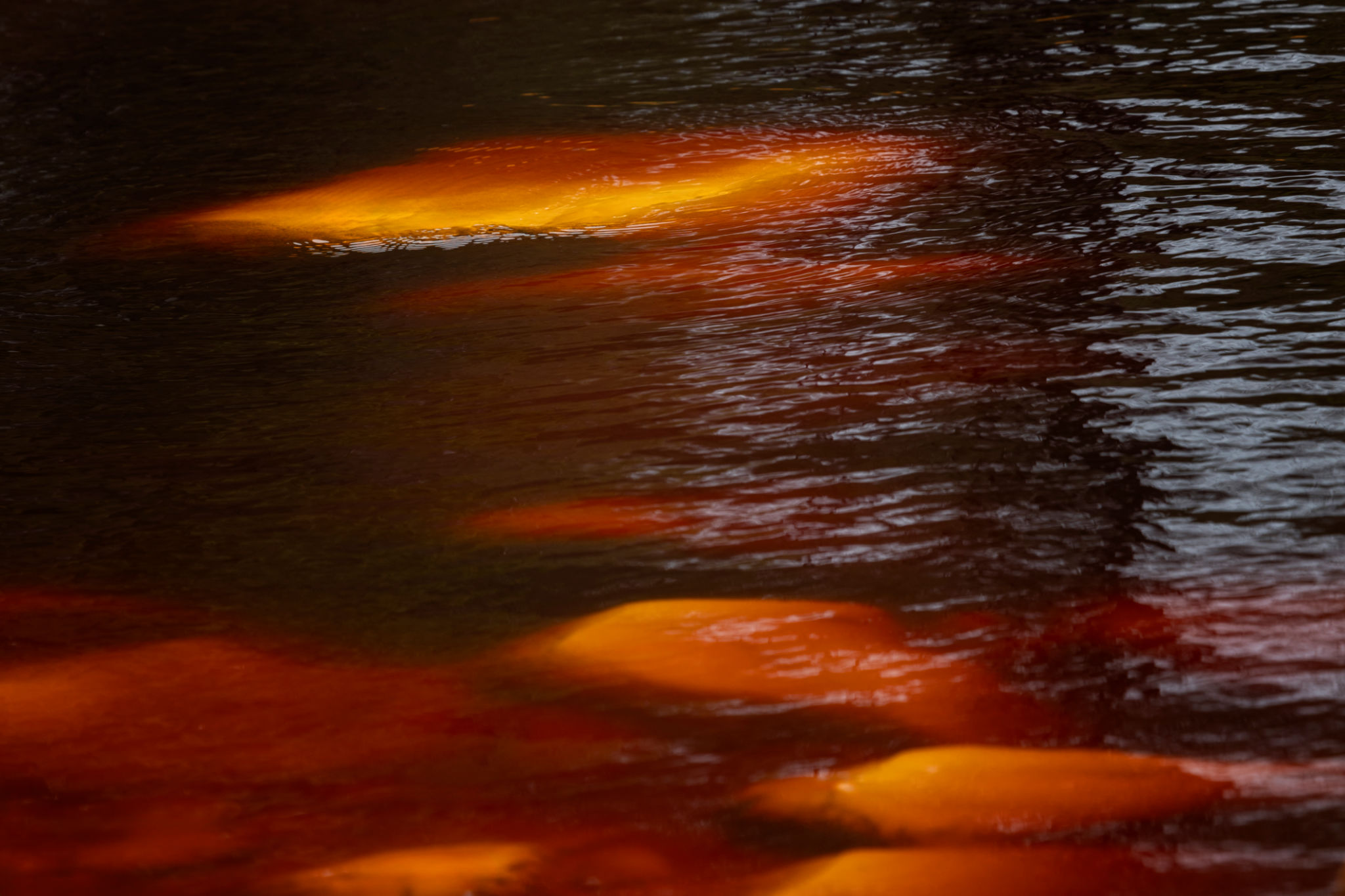
Step 4: Inspection and Evaluation
After applying the ferrous particles, the next step is to conduct a thorough inspection under appropriate lighting conditions. This often involves using a UV light if fluorescent particles are used, as it can enhance visibility of the indications. Inspectors carefully examine the component for any signs of particle accumulation indicating potential defects.
It's essential for inspectors to have a keen eye and experience in identifying genuine indications from false positives caused by factors such as excess magnetization or particle contamination.
Step 5: Demagnetization and Cleaning
Upon completing the inspection, it's crucial to demagnetize the component to prevent it from attracting debris during its service life. Demagnetization involves gradually reducing the magnetic field strength until it is negligible. This step helps restore the component to its normal state.
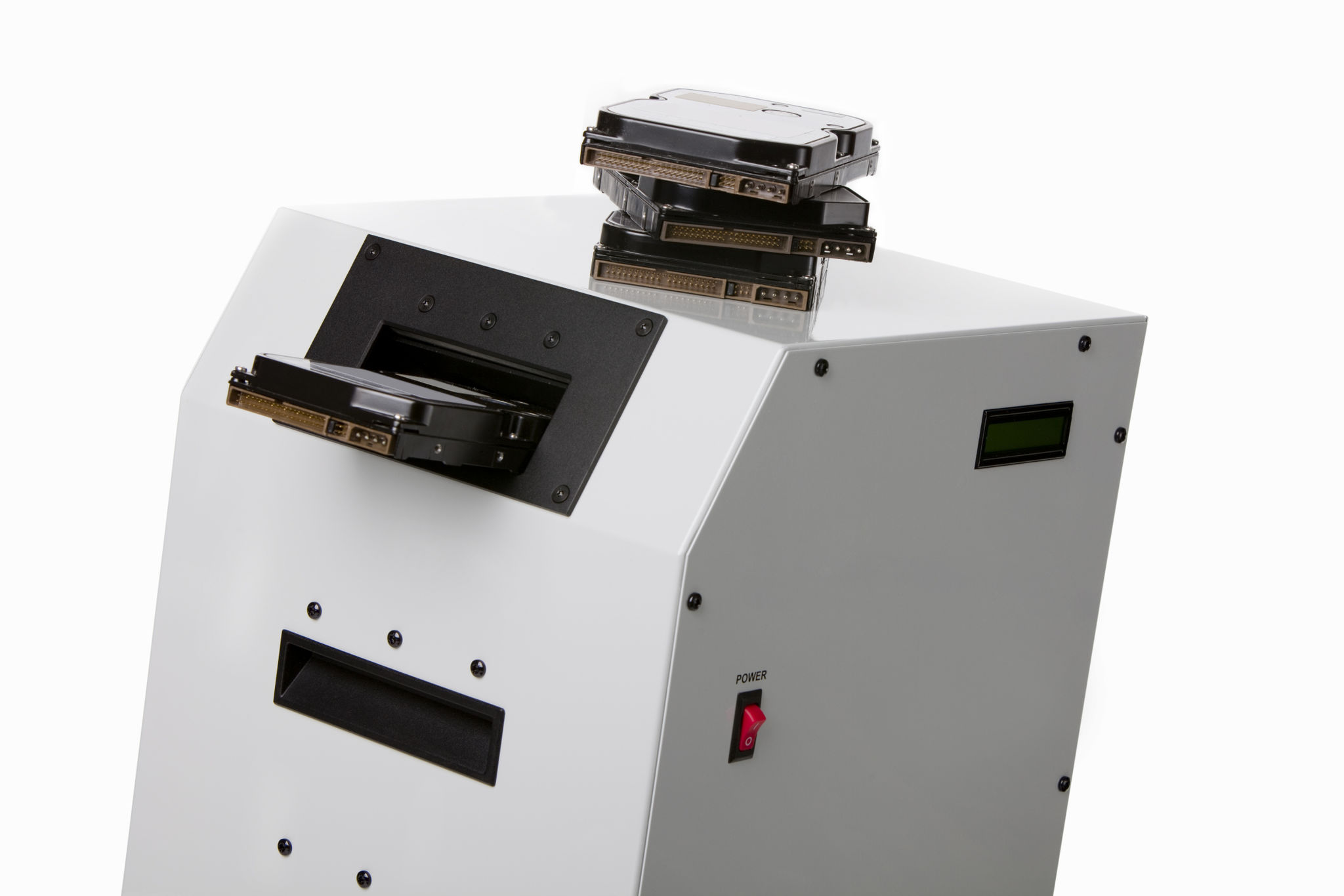
Finally, all remaining ferrous particles must be cleaned off the component's surface. This ensures that no residual particles are left behind that could cause issues during further manufacturing processes or in service.
Conclusion
Magnetic Particle Testing is a vital process in ensuring the reliability and safety of ferromagnetic components. By following these steps meticulously, inspectors can accurately identify defects that might compromise structural integrity. Whether you're involved in quality control or simply interested in non-destructive testing methods, understanding MPT is an invaluable skill in today's industrial landscape.