Top 5 Misconceptions About Radiographic Testing
Pr
Understanding Radiographic Testing
Radiographic testing (RT) is a crucial non-destructive testing (NDT) method used across various industries to inspect the internal structure of materials. Despite its importance, several misconceptions can cloud its understanding. This post aims to debunk some of the most common myths surrounding radiographic testing.
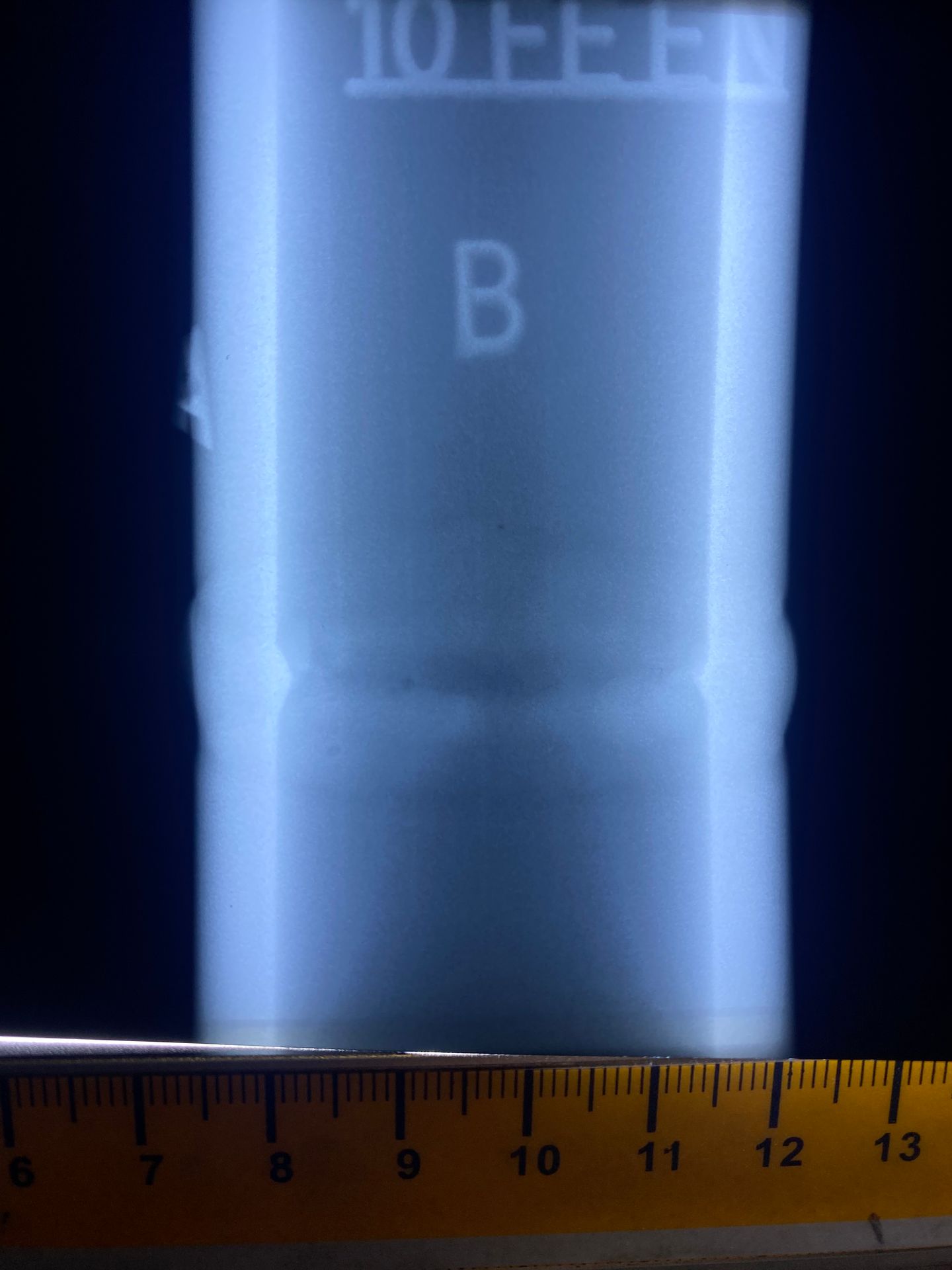
Misconception 1: Radiographic Testing is Unsafe
One of the most prevalent myths is that radiographic testing is inherently dangerous due to the use of radiation. In reality, RT is conducted under strict safety protocols and guidelines set by regulatory bodies. Technicians are well-trained in handling equipment and ensuring that radiation exposure is kept to a minimum, making RT a safe procedure when conducted properly.
Moreover, advancements in technology have significantly improved the safety measures associated with radiographic testing. Modern equipment is designed with protective features that further minimize any potential risks, ensuring the safety of both operators and the environment.
Misconception 2: RT is Only for Metal Inspection
While radiographic testing is commonly associated with the inspection of metallic materials, it is not limited to this application. RT can be used on a variety of materials, including plastics, composites, and ceramics. This versatility makes it an invaluable tool in industries ranging from aerospace to construction.
Radiographic testing's ability to assess different materials ensures that companies can maintain high standards of quality and safety across diverse applications. This broad applicability is often underestimated, leading to the misconception that RT is only beneficial for metal inspection.
Misconception 3: Results are Slow and Inefficient
Another common misconception is that radiographic testing is a slow and inefficient process. While traditional methods may have taken longer, modern radiographic techniques have significantly reduced the time required for inspection. Digital radiography, for instance, provides faster results with enhanced image quality, allowing for quicker analysis and decision-making.
The efficiency of RT today means that it can be seamlessly integrated into production schedules without causing significant delays. This rapid turnaround time is essential for industries that rely on fast-paced operations.
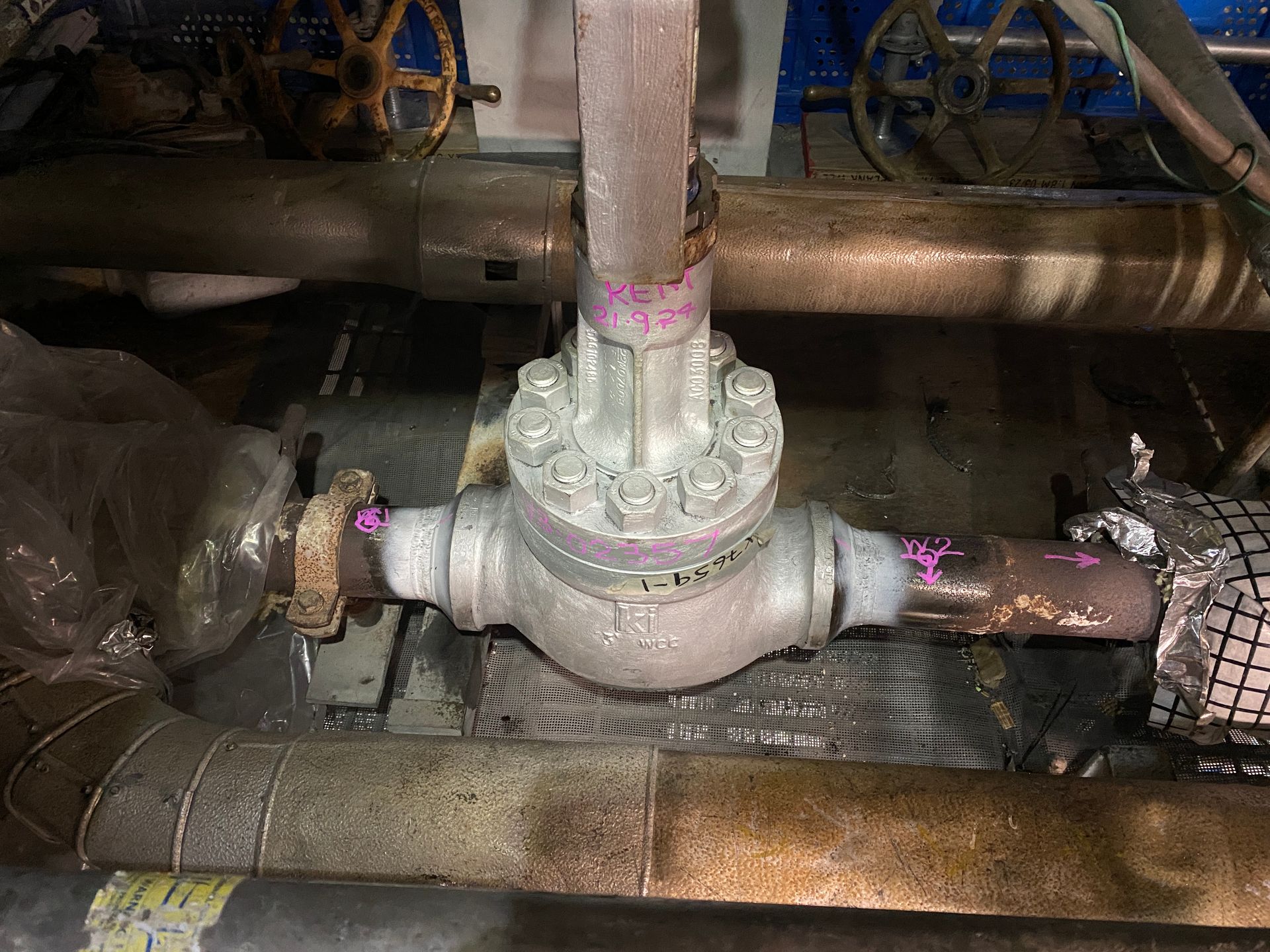
Misconception 4: RT is Expensive
Cost concerns often deter companies from utilizing radiographic testing, under the misconception that it is prohibitively expensive. While initial investments in equipment and training might be significant, the long-term benefits of preventing failures and ensuring product integrity far outweigh these costs.
By identifying defects early in the manufacturing process, radiographic testing helps avoid costly repairs and replacements down the line. This proactive approach ultimately saves money, making RT a cost-effective solution in the long run.
Misconception 5: Only Experts Can Interpret Results
It's often believed that only highly specialized experts can interpret radiographic test results. However, advancements in software and imaging technology have made it easier for trained technicians to analyze results effectively. Many modern systems include user-friendly interfaces and automated features that assist in result interpretation.
This democratization of data interpretation means more professionals can engage with radiographic testing without needing extensive specialization. Nevertheless, it remains crucial for personnel to receive proper training to ensure accurate analysis.
In summary, while misconceptions about radiographic testing persist, understanding the reality of this powerful inspection method reveals its safety, versatility, efficiency, cost-effectiveness, and accessibility. As industries continue to evolve, radiographic testing will remain an integral part of ensuring quality and safety across various applications.