The Future of Non-Destructive Testing: Emerging Trends and Technologies
Introduction to Non-Destructive Testing (NDT)
Non-Destructive Testing (NDT) has become an integral part of industries that require quality assurance while ensuring safety and reliability. Unlike traditional testing methods that often involve damaging the materials, NDT allows for the examination of materials, components, or assemblies without causing harm. This capability is crucial in fields such as aerospace, automotive, and construction, where the integrity of materials is paramount.
As technology continues to evolve, so does the landscape of NDT. Emerging trends and cutting-edge technologies are shaping the future of this vital industry. In this blog post, we will explore some of the most promising developments in NDT.
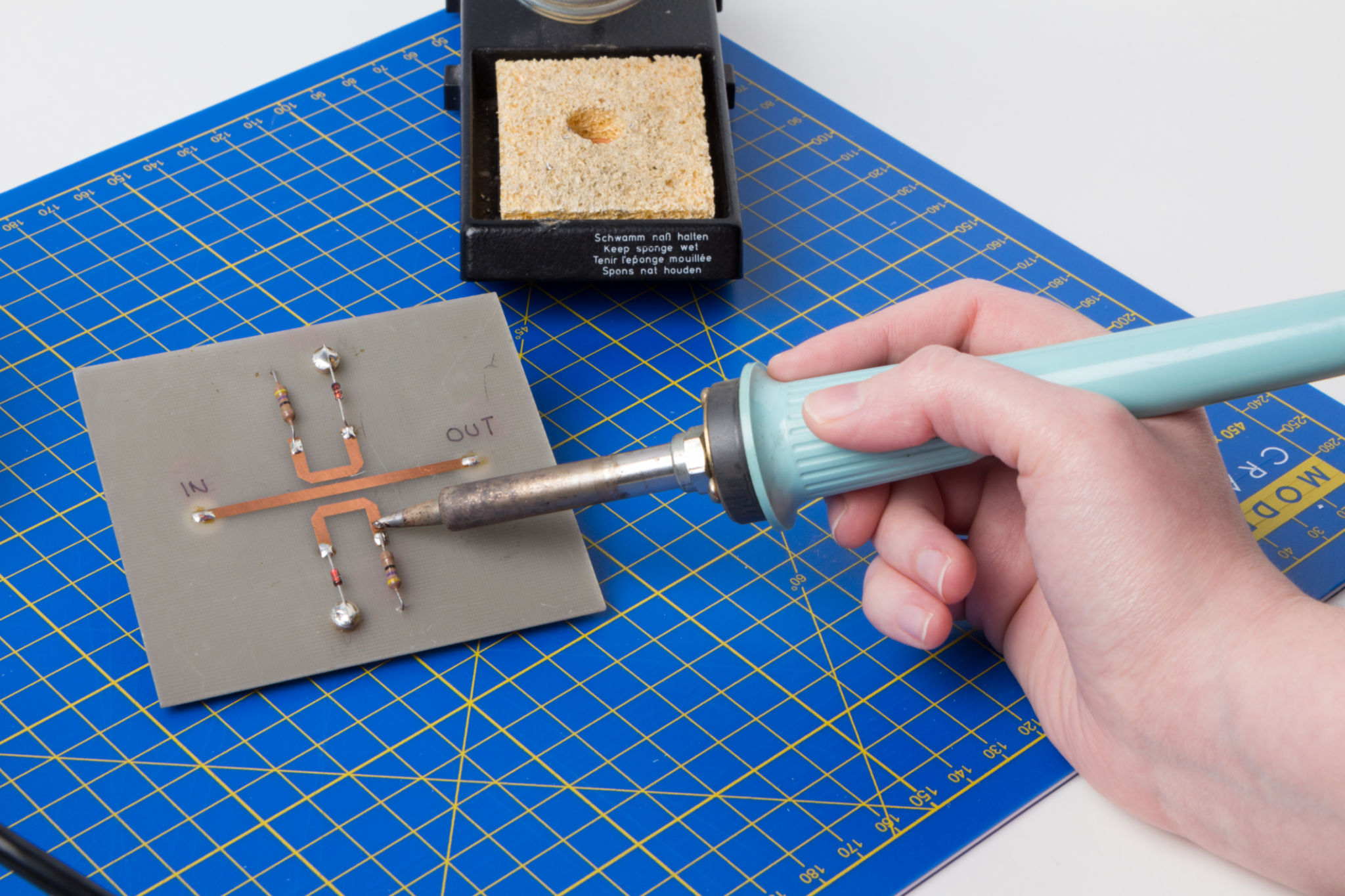
Advanced Imaging Techniques
One of the significant advancements in NDT is the development of advanced imaging techniques. Technologies such as computed tomography (CT) and digital radiography are becoming more prevalent. These methods provide highly detailed images, allowing for more accurate assessments of materials and structures. CT scanning, for instance, offers 3D imaging capabilities that were once unimaginable in the field of NDT.
These advanced imaging techniques not only improve the accuracy of inspections but also reduce the time and cost associated with testing. As a result, industries can make more informed decisions faster, leading to enhanced productivity and safety.
Ultrasonic Testing Enhancements
Ultrasonic testing has long been a staple in NDT due to its non-invasive nature and effectiveness. Recent enhancements in this area include the use of phased array ultrasonic testing (PAUT). PAUT offers significant improvements over traditional ultrasonic methods by using multiple elements to steer, focus, and scan beams for detailed inspections.
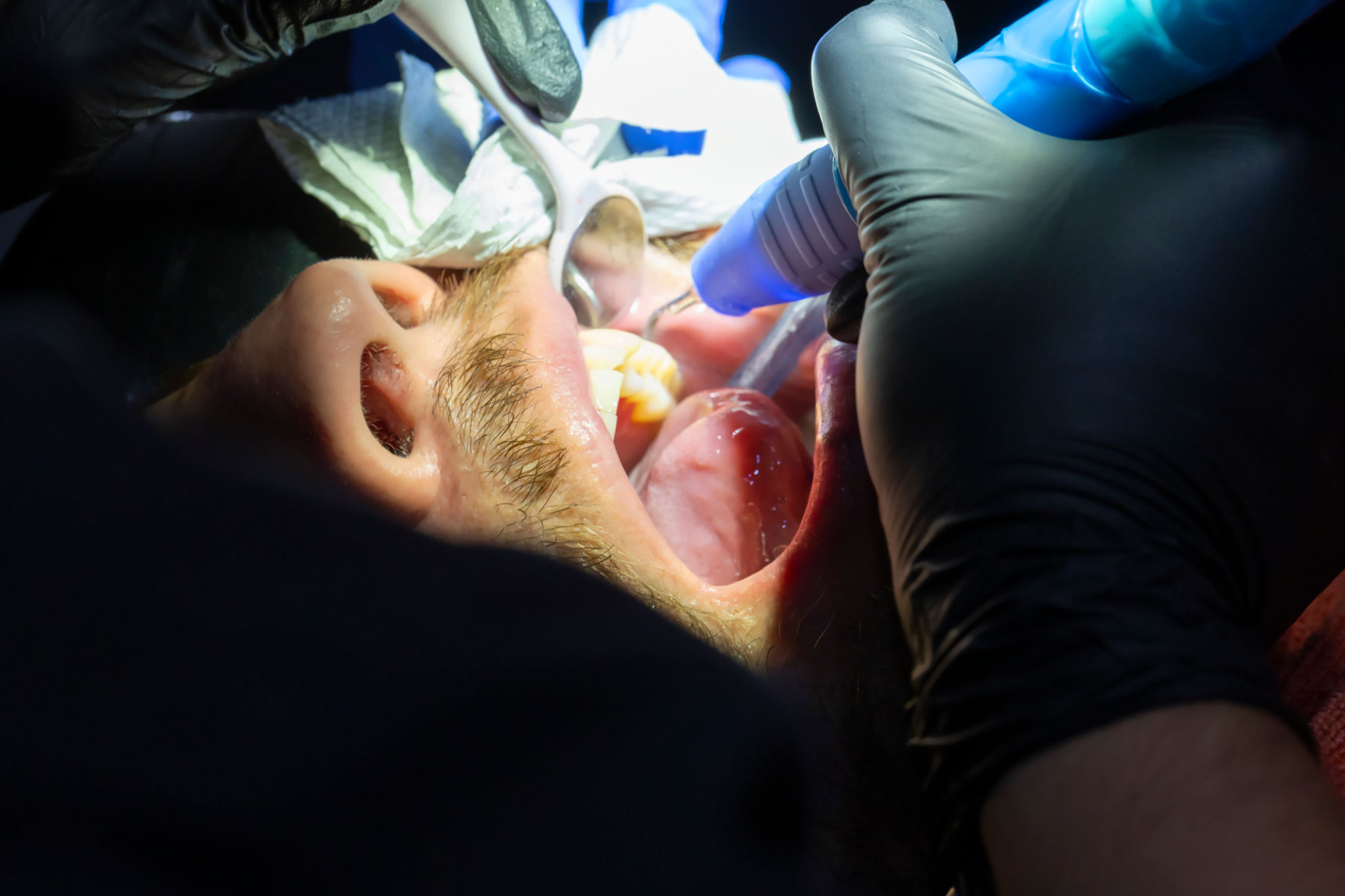
Integration of Artificial Intelligence
The integration of Artificial Intelligence (AI) into NDT processes is a game-changer. AI algorithms can analyze data more efficiently than human operators, identifying patterns and anomalies that might otherwise go unnoticed. This capability is especially valuable in industries where precision and accuracy are critical.
Machine learning models can be trained to recognize defects in images or data sets, leading to faster and more accurate diagnostics. As AI technology continues to advance, its role in NDT is expected to grow, providing even greater insights and efficiencies.
Development of Robotics in NDT
Robotics is another area that is transforming NDT. Robotic systems can perform inspections in hazardous or hard-to-reach environments, ensuring safety while maintaining thoroughness. These systems can be equipped with various sensors and tools to conduct a wide range of tests, from ultrasonic to visual inspections.
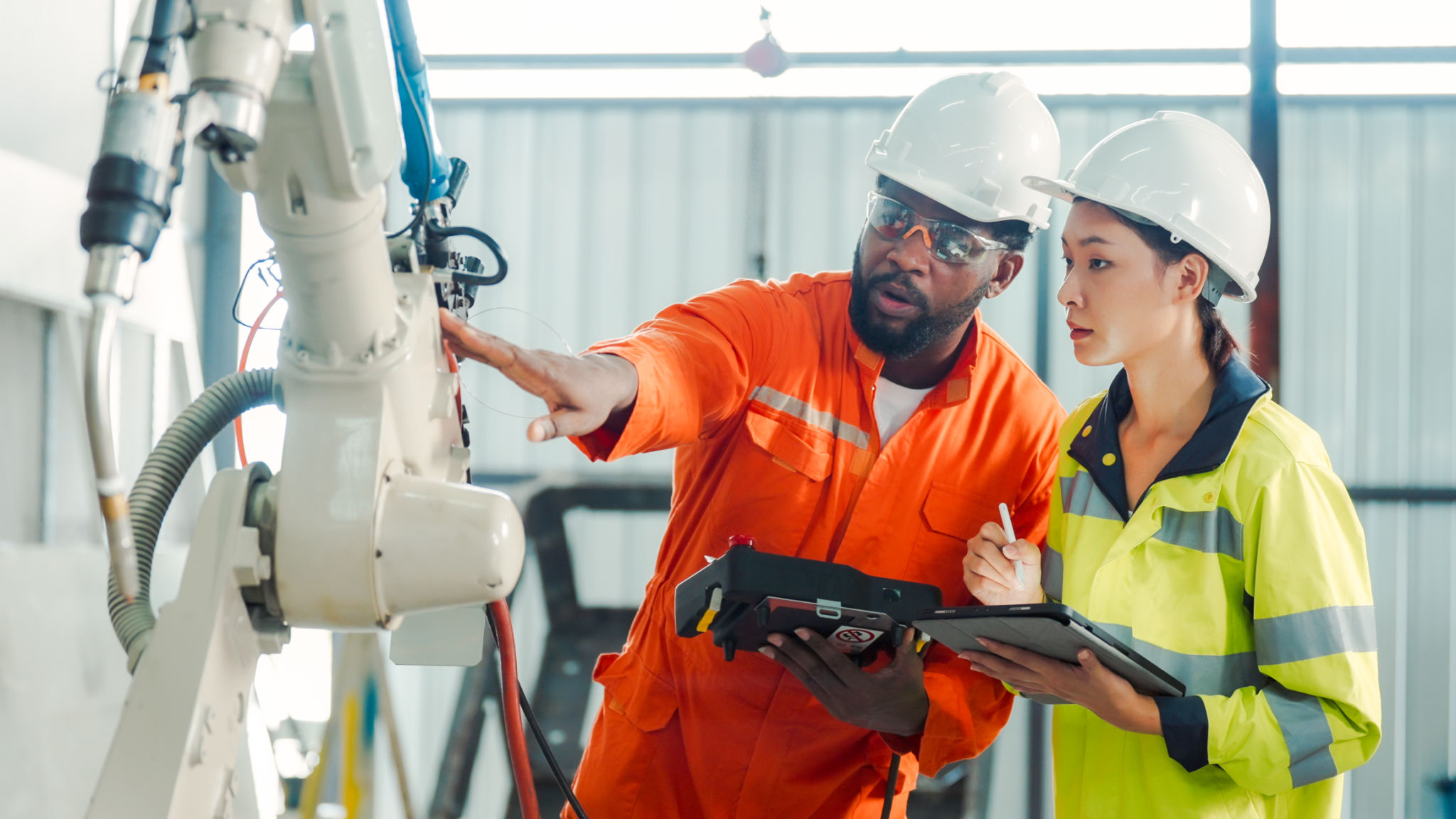
Remote Monitoring and Real-Time Data
The future of NDT is also leaning towards remote monitoring and real-time data acquisition. With the advent of IoT (Internet of Things) technology, sensors can continuously monitor the condition of structures or components. This capability allows for real-time data collection and analysis, enabling proactive maintenance strategies.
Real-time monitoring not only helps in preventing failures but also extends the lifespan of critical assets. By addressing issues before they become significant problems, industries can save on repair costs and avoid potential downtimes.
Sustainability in NDT
Sustainability is becoming an essential consideration in all industries, including NDT. The focus is shifting towards developing environmentally friendly testing methods that minimize waste and energy consumption. Emerging technologies are being designed with sustainability in mind, ensuring that NDT remains a viable option for future generations.
As we move forward, it is clear that the future of non-destructive testing holds exciting possibilities. By embracing these emerging trends and technologies, industries can ensure the continued safety, reliability, and efficiency of their operations.