Comparing NDT Techniques: Finding the Right Solution for Your Project
Pr
Understanding Non-Destructive Testing (NDT)
Non-Destructive Testing (NDT) is an essential process in various industries, allowing for the evaluation of materials, components, or assemblies without causing damage. This technique ensures that products meet quality standards while maintaining their integrity. NDT is critical in industries like aerospace, construction, and manufacturing, where safety and reliability are paramount.
Several NDT methods are available, each with its unique benefits and limitations. Choosing the right technique for your project can significantly impact the outcome, ensuring accuracy, safety, and cost-effectiveness. Understanding the differences between these techniques is crucial for making an informed decision.
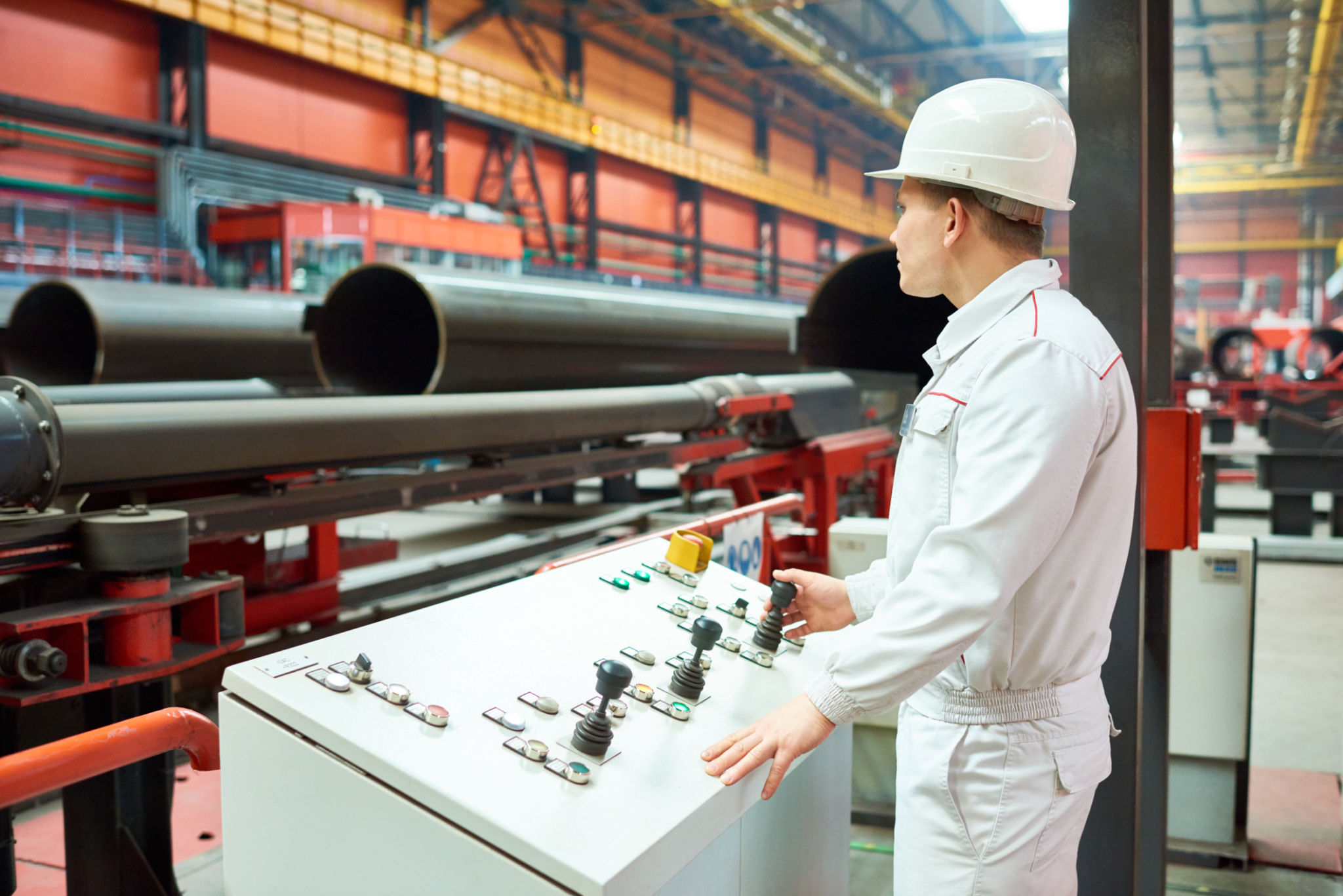
Common NDT Techniques
Ultrasonic Testing (UT)
Ultrasonic Testing is a popular NDT method that uses high-frequency sound waves to detect imperfections in materials. By transmitting these waves through the material, defects such as cracks or voids can be identified based on the reflection of the waves. **Ultrasonic Testing** is highly effective for inspecting metals, composites, and welds.
This technique is known for its deep penetration capabilities and high sensitivity to small defects. However, it requires skilled technicians and can be less effective on rough surfaces or materials with complex geometries.
Radiographic Testing (RT)
Radiographic Testing employs X-rays or gamma rays to examine the internal structure of a component. The process involves capturing images on radiographic film or digital detectors, allowing for the detection of internal defects such as voids or inclusions.

This method provides a permanent record and is excellent for inspecting a wide range of materials. However, it involves radiation exposure, requiring stringent safety measures and specialized equipment.
Magnetic Particle Testing (MT)
Magnetic Particle Testing is used to detect surface and near-surface defects in ferromagnetic materials. The process involves magnetizing the component and applying ferrous particles to identify discontinuities. **MT** is particularly effective for detecting surface cracks in castings and welds.
While it is a fast and relatively simple technique, it is limited to ferromagnetic materials and may not detect subsurface defects effectively.
Factors to Consider When Choosing an NDT Technique
Selecting the right NDT technique depends on several factors, including the type of material being tested, the nature of potential defects, and the required sensitivity level. Consider the following when making your choice:
- The material composition and structure
- The size and location of potential defects
- Cost and availability of equipment
- Safety requirements and regulations
Project-Specific Requirements
Each project may have unique requirements that influence the choice of NDT technique. For instance, some projects may prioritize speed over sensitivity, while others may require detailed documentation of findings. Collaborating with NDT professionals can help tailor the testing process to meet specific project needs.

The Importance of Skilled Technicians
The effectiveness of any NDT technique largely depends on the skill and experience of the technicians performing the tests. Ensuring that your team is well-trained and certified can significantly enhance the reliability of the testing process. Investing in ongoing training and certification programs helps keep technicians updated on the latest advancements in NDT technology.
In conclusion, selecting the right NDT technique is vital for ensuring the safety and integrity of your projects. By understanding the strengths and limitations of each method, considering project-specific requirements, and employing skilled technicians, you can make informed decisions that lead to successful outcomes.