Busting Myths: Common Misconceptions About Non Destructive Testing
Pr
Understanding Non-Destructive Testing
Non-Destructive Testing (NDT) plays a vital role in various industries by ensuring the integrity and reliability of materials and structures without causing any damage. Despite its importance, there are several misconceptions surrounding NDT techniques that can lead to misunderstandings about their applications and effectiveness. In this post, we aim to bust some common myths about Non-Destructive Testing.

Myth 1: NDT is Only for Large-Scale Industries
A common misconception is that Non-Destructive Testing is only applicable to large-scale industries such as aerospace or oil and gas. While it is true that these sectors heavily rely on NDT, many other fields also benefit from these techniques. From small manufacturing companies to art restoration projects, NDT provides valuable insights into material conditions without causing damage, making it suitable for any industry that requires quality assurance.
Small businesses in construction, automotive, and even electronics utilize NDT methods to ensure their products meet safety and quality standards. This versatile technology offers solutions for both large corporations and smaller enterprises seeking reliable testing methods.
Myth 2: NDT Methods Are Too Expensive
Another myth that persists is the belief that NDT methods are prohibitively expensive. In reality, investing in NDT can be cost-effective in the long run. By identifying potential issues early on, companies can avoid costly repairs, replacements, and downtime. The expense of NDT is often outweighed by the savings gained from preventing failures and maintaining safety standards.

Additionally, advancements in technology have made NDT equipment more accessible and affordable. Companies can now choose from a variety of testing methods that fit their budget without compromising on quality or accuracy.
Myth 3: All NDT Techniques Are the Same
It's easy to assume that all Non-Destructive Testing techniques offer the same results, but this is far from the truth. There are numerous NDT methods available, each with its own unique applications and benefits. From ultrasonic testing and radiography to magnetic particle testing and eddy current testing, each technique is designed to address specific types of materials and defects.
Choosing the right method depends on factors such as the material being tested, the type of defect being detected, and the environment in which testing is conducted. Understanding these differences is crucial for selecting the most appropriate NDT method for a given situation.
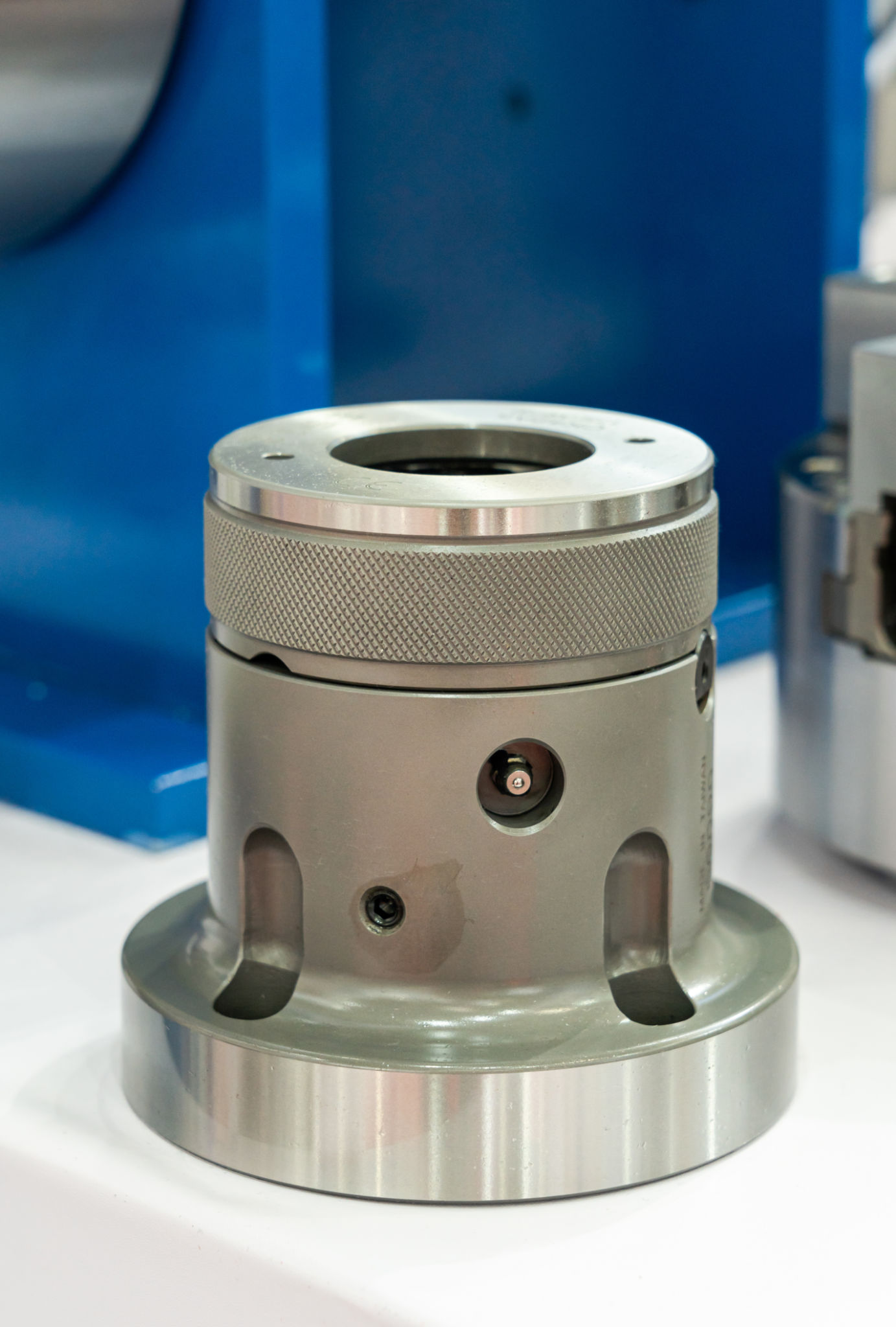
Myth 4: NDT Requires Extensive Downtime
Some believe that implementing NDT means halting operations for an extended period. However, many NDT methods are designed to be quick and efficient, allowing for minimal disruption to regular processes. Techniques such as ultrasonic testing can often be performed on-site without requiring a shutdown of operations.
This misconception stems from traditional testing methods that often necessitated significant downtime. Modern NDT techniques are continually evolving to provide faster and more efficient testing solutions.
Myth 5: NDT Is Only for Detecting Surface Defects
While some NDT techniques are indeed suited for surface defect detection, many others can identify internal flaws that are not visible to the naked eye. For instance, radiography and ultrasonic testing penetrate deep into materials to uncover hidden defects.
This capability makes NDT an invaluable tool for industries where safety and reliability are paramount. By offering insights into both surface and internal conditions, NDT helps ensure the longevity and performance of critical components.
Conclusion
Non-Destructive Testing is an essential tool across various industries, offering numerous benefits beyond the common misconceptions. By understanding the truth behind these myths, businesses can better leverage NDT technologies to enhance safety, quality, and efficiency. As technology advances, NDT will continue to play a crucial role in maintaining the integrity of materials and structures worldwide.